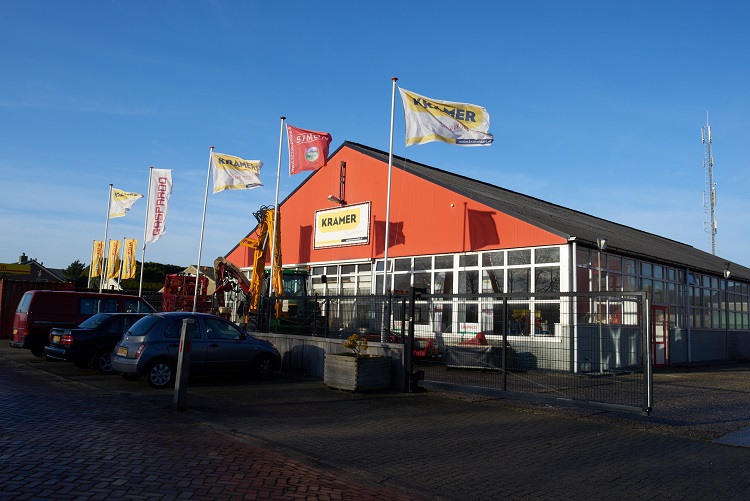
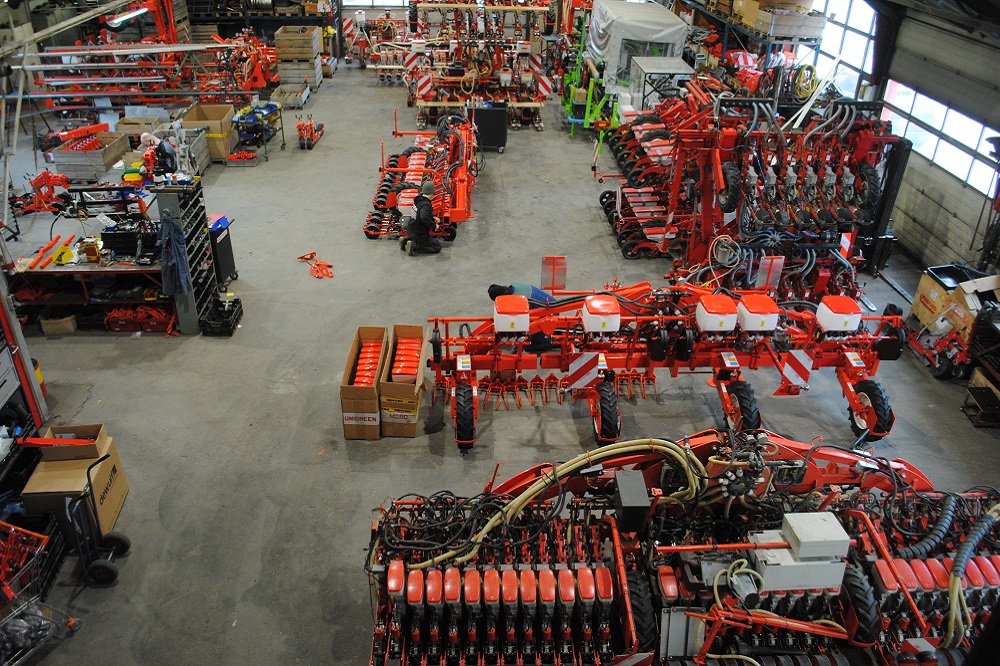
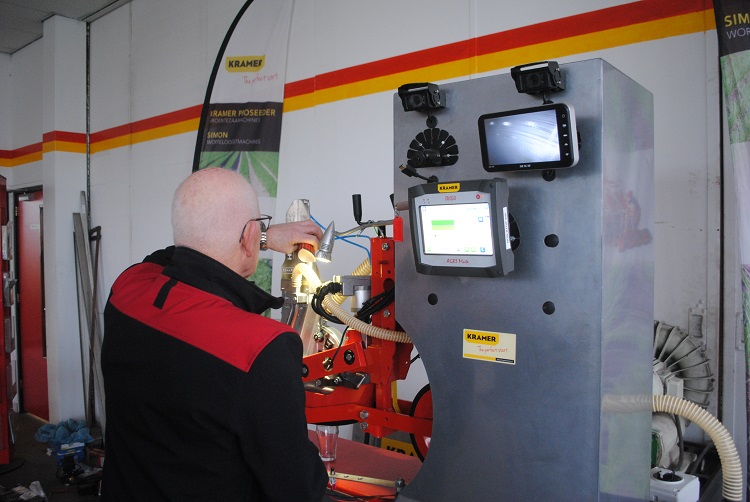
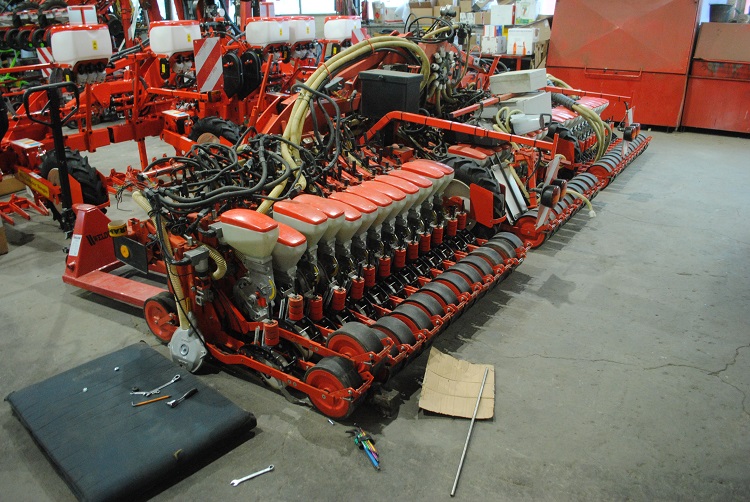
About us
Kramer is importer for the Kramer Proseeder vegetable seeders for Europe. Made by Gaspardo. Our precision seeders are suitable for sowing carrots, onions, red beets, chicory and other fine-seeded crops. We are also importer of the Simon carrot harvesters for the Benelux.
Kramer. The perfect start
Growing vegetables is precision work and requires craftsmanship and the best machinery. Kramer specializes in optimizing machinery for growing vegetables. Driven by perfectionism, Kramer offers unique solutions for sowing and harvesting crops such as carrots, onions and chicory. According to Kramer, a good start is not good enough. The best results require the best machines. That starts at Kramer: The perfect start.
The realization that a perfect start yields a great deal is what drives Kramer’s specialists to help entrepreneurs around the world to start the crop. To this end, Kramer develops and supplies the most advanced seeding machines and can help entrepreneurs with a great deal of knowledge and insight into crop start.
Meet Kramer ...
How do you get the seed into the seedbed in the right way so that the grower ultimately benefits from the most uniform emergence of his crop? It is the question that occupies the people at Kramer BV on an almost daily basis. They are constantly looking at future developments such as camera techniques, ribbon seeding, fewer rows on a bed, variable seeding and variable depth controls. The Kramer ProSeeder is always adapted to individual needs and circumstances. The result of this working method is that no identical machine leaves the production hall in Bant. All stem from Kramer’s renowned philosophy. “The better the seed is pressed, the better the result.”
“The answer to a question from an individual grower about problems from the field often does not come from the factory. That is precisely where our strength lies,” says co-owner Reinoud Tepper of Kramer BV, while being advised by senior consultant Thijs Kramer Who demonstrates the principle of a non-stop seeder, which is being developed for a trial field machine of onion seed specialist De Groot en Slot. The seed is vacuum sucked towards the disc.
By means of the emptying suction technique and coating, even a single seed is prevented from mixing, before the seed is placed in the right place with GPS. “Purely intended for the trial field, but actually all our techniques do come together in this machine. We deliberately choose vacuum and not a compressor, because you don’t want moisture with your seed. The drive is electric. We now know very well how to use camera technology. We also have machines running that capture 36 images at a time. Our widest machine was nine meters with thirty elements,” Kramer says.
The perfectionism required for growing vegetables such as carrots, onions, red beets, chicory and other fine-seeded crops is also reflected in the Kramer Proseeder seeders. “In the end, it’s all about getting the crops off to a good start, The Perfect Start as we have been calling it for the past eight years,” explains Van der Wekken. The basis of the machine is Maschio Gaspardo seeder, which comes to Bant as a semi-finished product. There, each version is customized to the needs of the Dutch grower.
“Where factory stops, we start”
The specialty in vegetable sowing machines originated from the hobby of Thijs Kramer. Initially as an importer of the French Nodet. After the takeover by Kuhn, the importership expired. Moreover, the French lifted their production line, forcing Kramer to look for another seeder. That ended up being Maschio Gaspardo. “Because we could start delivering directly and ex factory,” Thijs Kramer looks back, “Eventually it grew into a specialty. Where the factory stops, we start. After all, a vegetable seeder is often seen as one of 25 variants of a seeder. That is precisely where our strength lies. We continue where a grower gets stuck at the factory or mechanization company with a problem in the field in other places. We do nothing but vegetable seeders.”
Sowing result through pressure wheel
Perhaps the real turning point in Kramer BV’s development came at a trial field of Potato Europe, the potato event held in Emmeloord in 2000. Van der Wekken: “Everyone there was allowed to sow under poor conditions. The best sowing results were achieved by the machines, which are heavy by themselves. That got us thinking. So it’s about the seed carrying enough weight when it goes into the ground. That’s where the idea comes from with the wheels fitted with pin weights. These push the seed into the ground and move independently of the parallelogram. That’s what sets us apart. It’s not space technology, but ultimately this is what it’s all about. You have to press the seed into the ground with equal weight, so that it gets to the right place to absorb the moisture properly and starts germinating.”
The secret behind Kramer’s proven concept lies mainly in the pressure wheel.
Custom made
Kramer extends the seeding salters, allowing the loose soil to fall onto the seed only after the pressure wheel has pressed it down. The wheel can be made of steel or plastic. Pins ensure that the seed is properly distributed on the coulter. The front piece of the coulter can be interchanged with three different pre-openings of 8, 15 and 25 millimeters to correctly place the seeds in the “furrow. The seeding housing can be made in different ways to use the right components for each seeding method. “All custom made,” he says.
“Where people used to say ‘seeding in rows,’ it’s different now. You can eliminate a lot. Misses you don’t want. That’s why we came up with the electric drive, which allows you to speed up if there’s a miss in between. The next step is seed counting, so you can put that in other distances as well.” Everything is tracked with cameras, so the grower doesn’t have to get off the tractor during seeding. A lot safer, too.
“We got that demand from the market about ten years ago and have been running the seeding machines with cameras ever since,” Van der Wekken says, “Especially when seeding onions, where you saw a lot of two men working on behalf of the contractor. They stood on the back of the machine and kept an eye on whether a disc was empty. With the camera, we wanted to see the misses or doubles in the cab. It started with four rows. Now we have another machine for a German wheel driver in the assembly hall, taking 33 images. Those come into the computer. You click on an image and see exactly what’s happening on the disk. Theoretically, you could also put cameras on the back of the machine, monitoring everything.”
Kramer BV’s widest machine running in Zeeland is 9 meters, 6 by 150 centimeters. “This vegetable grower sows with a crawler tractor. Another grower chooses Kramer because he sows very expensive seed. Think of asparagus and leeks. There it really comes down to sowing results.” The radish grower in Germany, 33 rows is also a reference that people in Bant are very proud of. “He, too, benefits from a uniform lot. The turnout has to be completely one hundred percent.”
Better and more uniform product
Today, Van der Wekken sees that arable knowledge is increasing. Growers are working with GPS and performing soil scans. “What is still missing now is the translation. How do we use the data in the field to ultimately get a better and more uniform product. In the development of the seeder, the next step is to think about automatic depth control, electric and task card controlled. In which areas do I sow a little thicker and where less?”
Van der Wekken knows that there are growers, who already sow very consciously by coarseness. “If you then go from 3.6 to 3.2 units, that results in savings. In other places, it might make sense to actually sow thicker for a higher yield. And why do we always sow five rows in a bed? If you lift the middle element you give the seed more space. Everyone knows that on the sides the thickness onions grow.”
Trial of ribbon seeding
Kramer BV also participated in a trial of ribbon seeding. Although this development is still in the research phase , Van der Wekken says it is the future. “It is unfortunate that the first trials in Nagele did not turn out well, but we have now also seen that chicory in combination with less or no irrigation there are nice results. Nice side effect is also that the paper keeps weeds under it. Especially in organic this is crucial. The technology may not be mature enough yet, but this is where we are headed in the coming decades.”
In any case, the Bant-based company will continue making customized solutions for vegetable growers. That also automatically means pioneering and innovating. “Sowing depth, sowing distance, amount of seeds per hectare, the number of rows, the right sowing coulter, the toeing of the sowing trench, the pressure weight. We like to think with you to arrive at the appropriate solution.”